Hotline
+86-13692841862
Email:info@mayflay.com
Add::NO.289,Guangreng Rd,Xiaojinkou Str.Huicheng Dis,Huizhou City,Guangdong Province,China.
Surface Treatment Equipment
Coil Handling Equipment
Solutions
Application
About us
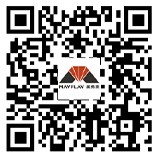
welcome to MAYFLAY
For consultation/feedback, please call the service hotline: +86-13692841862 Email:info@mayflay.com
There are many types of shot blasting machines.Different types of shot blasting machines are used according to different products and environments. The hook type shot blasting machine is a common shot blasting machine.
The hook type shot blasting machine is a kind of cleaning equipment that throws high-speed steel shots from the shot blasting device on the surface of the workpiece. The shot circulation system is composed of a feeding screw, a hoist, a separator, a steel shot control system, a hopper, etc.
The following are the reasons why the steel shot circulation system of the hook type shot blasting machine is not smooth.
First of all, it may be that the hoist belt is slack and the hoist belt is slipping.
Second, it may be that the steel shot transport tube is blocked due to the pellets agglomerated.
Third, there may be a gap in the steel shot storage bin, which reduces the amount of steel shot circulating.
Fourth, it may be that the steel shot retracting scraper is worn out.
Fifth, it may be that the screw conveyor is stuck.
At last, it may be that there are too many impurities in the trommel, which block the sieve holes and affect the steel shot to pass through the sieve.
MAYFLAY is a high quality manufacturer of all types of surface preparation equipment and coil handling equipment.It has long been committed to the design and manufacture of shot blasting, shot peening, sandblasting and decoiler, straightener, feeder and press machine,and provides intelligent surface treatment solutions and sheet metal stamping solutions to customers around the world.
MAYFLAY has strong scientific and technological innovation capabilities, and establish a new model for joint development with well-known universities and benchmarking companies in the automobiles industry.
Roller Conveyor shot blasting machine
Roller conveyor shot blasting machine is built to clean steel plates and profiles. They are mostly used for descaling, derusting, paint removal, paint preparation, deburring and general surface preparation prior welding, cutting, machining and burning operations.
technical consultation
AddThis Sharing Buttons
Share to FacebookShare to TwitterShare to PinterestShare to LinkedInShare to 更多...3
Brief Profile
Roller conveyor shot blasting machines, specially designed for constant and continuous blasting of de-scaling, de-sanding, cleaning and pre-treatment for different type of steel, like steel plates, steel girder, shape steel, structural steel, steel pipe, steel castings etc. It is usually long and giant but compact, configurable with 4-16 sets of blast wheels and even more to meet different requirements of surface cleaning and strengthening.
The transport system is the rollers conveyor, driven steadily and stably by the chain and chain wheel and loaded with rollers of 80mm, 121mm, 180mm in diameter or even bigger, can load work pieces from 500KG to 2000KG and even heavier. Work pieces are loaded on the inlet of roller conveyor, being blasted in the blasting chamber, and come out from the outlet roller conveyor for unloading. continuous blasting process with one press of the button.
Load, roller transport, blast, unload. This is a through-type and continuous production line with high efficiency and an ideal option for surface cleaning of long and large steel materials, structural steel, steel welding part etc.
Applicable Work pieces
Transport system:Roller Conveyor
Surface condition before shot blasting: Rust, Scalings
Advised load weight per meter: 2000kgs
Number of Blast Wheels: 16 sets
Suitable Work pieces:Profiles, H beam, I Beam, C channels, Plate, Welded steel fabrications, Structural steel, transmission & television towers, Pipe and so on.
Automatic loading system can be customized
Can be equipped with painting line
Futures
Optimized design & economic solution
Ultimately compact design for easy operation and wide range of options of models to adapt to diversified production efficiencies and sizes of work pieces. Constant & continuous blasting process with high efficiency, saving abrasives with reliable performance of cleaning & dedusting and low costs.
Reliable quality & stable performance
Blasting machine body: 6-10mm thickness Manganese 13 steel plates well-welded in one piece and Manganese 13 steel protective boards, offering excellent wear resistance and protection from even the most aggressive blast media. Roller diameters, from 80mm to 180mm or even bigger and loading weight, from 500KG to 2000KG and even heavier, guarantee a long equipment life with a high uptime and low maintenance cost.
Stepless speed regulation is adopted for the roller conveying system to have stable and reliable operation and optimized blasting result on work piece.
High-end technologies applied
Optical grating detecting device is equipped in the front of the blasting chamber inlet to transmit time-lapse signal to the PLC as soon as work piece goes into the blasting chamber and gets ready for blasting process.
Compressed-air reverse-direction device, equipped in
the outlet roller segment, blows away the shots on the work piece and keeps work piece’s surface clean before it’s transported to the unloading roller segment.
Convenient control & maintenance
PLC control, all process parameters of work pieces blasting can be configured and saved in PLC control unit, in the result that repeat input, repeat pushing different buttons are completely unnecessary. This means, much shorter time of parameter configuration, much less working hours of operator and high efficiency.
Maintenance and examination windows are set on each core working parts of this machine for easy maintenance.
Special design of sealing
Blasting sealing: rubber segments are equipped at the roller conveyor inlet & outlet and the blasting chamber to make the machine sealing effect excellently and prevent accidents of shot spillage.
Care about environment
Great importance is attached by Mayflay to environment protection: noise and dust emission. We adopt high-end methods to reduce noise to 85DB and dust emission concentration to less than 50mg/m3 (these results can be even better with higher standard of configurations).
Main Parts
Blasting chamber system
a.6mm-10mm thickness Manganese 13 steel plates, accurately welded in one piece, and a line of 10mm Manganese 13 steel protective boards, installed at the area exposed to blasting shots stream, guarantee excellent wear resistance of the blasting chamber.
b.4-16 sets of blast wheels, equipped vertically and horizontally at both sides of the chamber, guarantees thorough cleaning of every work piece.
Multi-layer rubber sealing technique is used at the inlet chamber and outlet chamber to protect the side steel plates. Rubber segments sealing method make the machine sealing effect excellently and prevents accidents of shot spillage.
Roller conveyor system
a.Stepless speed regulation system is used for the whole transporting system for the work pieces to have stable and reliable operation and optimized blasting result on work piece.
b.The roller conveyor system is combined with three segments: inlet roller conveyor, blasting chamber roller conveyor and outlet roller conveyor.
High loading weight makes the roller conveyor system sustainable to heavy work piece and workload.
Screw conveyor system
a.2 or more screw conveyor systems, installed at the bottom of the blasting chamber and driven by the gear motor of the bucket elevator, consist of screw axle, blades and screw heads at both sides.
b.During working, the screw conveyor pushes the collected shots to the bottom of the bucket elevator and the shots are lifted by the buckets to the upper part of the elevator and pour into the shot separator.
1 screw conveyor system is installed at the top side of the bucket elevator to both push shots to the shots separator and separating partial dust and small broken shots through the rolling mesh sieve.
Bucket elevator system
a.The elevator system is built with steel plates by accurate soldering technique and driven by 1 gear motor at the top.
b.It includes, 2pcs high-quality wheel hubs, 1 elevator body, 1 high-performance and durable belt and several alloy buckets, providing the maximum transporting amount 130Ton/H. It collects and lifts those shots that are recycled by the screw conveyor, onto the separator and storage cabinet.
c.A window is designed on the elevator for easy maintenance and examination.
Separator system