Hotline
+86-13692841862
Email:info@mayflay.com
Add::NO.289,Guangreng Rd,Xiaojinkou Str.Huicheng Dis,Huizhou City,Guangdong Province,China.
Surface Treatment Equipment
Coil Handling Equipment
Solutions
Application
About us
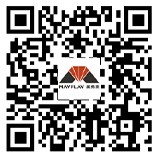
welcome to MAYFLAY
For consultation/feedback, please call the service hotline: +86-13692841862 Email:info@mayflay.com
A roller pass, Spinner Hanger Hook Type Shot Blasting Machine, a shot blasting room is equipped with a shot blasting device; the conveying roller table includes a feed conveying roller table, a shot blasting cleaning room roller table and a discharge conveying roller table, shot blasting cleaning The chamber roller table is located in the shot blasting cleaning chamber; the hook is driven by an electric hoist to make the hook travel and lift on the hanging rail; the bucket elevator has a material inlet and a material outlet, the material inlet and the lower horizontal screw conveyor Connection; the upper horizontal screw conveyor is connected to the discharge port; the pill sand separator has a separation area and an air inlet, and the separation area is connected to the upper horizontal screw conveyor; the dust collector is connected to the air inlet of the pill sand separator. The utility model applies strong shot blasting to the surface and inner cavity of the original metal component to remove rust spots, rust layer, welding slag and oxide scale on the surface, so that it has a uniform and uniform metallic luster surface with a certain finish, so as to Remove stress, improve the surface finish quality and corrosion resistance of the material.
1. A roller pass through, Spinner Hanger Hook Type Shot Blasting Machine, which is characterized by including: a shot blasting cleaning room, a plurality of shot blasting devices are installed on the outer wall; a conveying roller table, which includes sequentially connected and used to convey processing workpiece The feed conveyor roller table, shot blasting cleaning room roller table and discharge conveyor roller table, the shot blasting cleaning room roller table is located in the shot blasting cleaning room; hook; hanging rail; electric hoist, the hook is driven by the electric hoist Make the hook go up and down on the hanging rail; the lower longitudinal screw conveyor, one end of which is connected to the pellet outlet of the shot blasting cleaning room; the lower transverse screw conveyor, one end of which is connected to the other end of the lower longitudinal screw conveyor A bucket elevator, which has a material inlet and a material outlet, the material inlet is connected to the other end of the lower horizontal screw conveyor; the upper transverse screw conveyor, one end of which is connected to the material outlet of the bucket elevator; The shot sand separator has a separation area and an air inlet, which is connected with the other end of the upper horizontal screw conveyor; and a dust collector, which is connected with the air inlet of the shot sand separator and the shot blasting cleaning chamber.
Automotive Shot Blasting and Peening solutions
Sandblasting is to use compressed air to spray abrasive to the surface of workpiece at high speed. The purpose of sandblasting is to improve the appearance quality of workpiece surface by removing oxide layer and rust. Shot peening is to make the high-speed hard particles (generally steel particles) hit the surface of metal workpiece, in order to improve the fatigue strength of metal surface. Sand blasting and shot blasting are two different processes and different tools are used. However, both of them can be recycled.
The technology of shot blasting cleaning machine replaces the common cold and hot forming process to form large thin-walled aluminum parts, which can not only avoid the residual tensile stress on the surface of the parts, but also obtain the favorable compressive stress for the parts.
It should be noted that the service temperature of the parts treated by shot blasting machine should not be too high, otherwise the compressive stress will disappear automatically at high temperature, thus the expected effect will be lost. Their service temperature is determined by the material of the parts, which is about 260-290 ℃ for general steel parts and 170 ℃ for aluminum parts.